hazardous Area
Our electrical system designs for hazardous areas where explosive atmospheres may be present can ensure maximum safety and compliance with both national and international standards, thereby protecting workers and the environment from potential explosive hazards.
Did you know that flour, sugar and cocoa are highly explosive and come under the heading of “combustible dusts”? Some of the worst industrial explosions have been due to combustible dusts.
A household light switch may emit a small, harmless visible spark when switching. In an ordinary atmosphere this arc is of no concern, but if flammable vapour or dust is present, the arc might start an explosion. Electrical equipment intended for use in a chemical factory, oil refinery, flour or grain mill is designed either to contain any explosion within the device, prevent ingress of the hazardous substance or is designed not to produce sparks with sufficient energy to trigger an explosion.
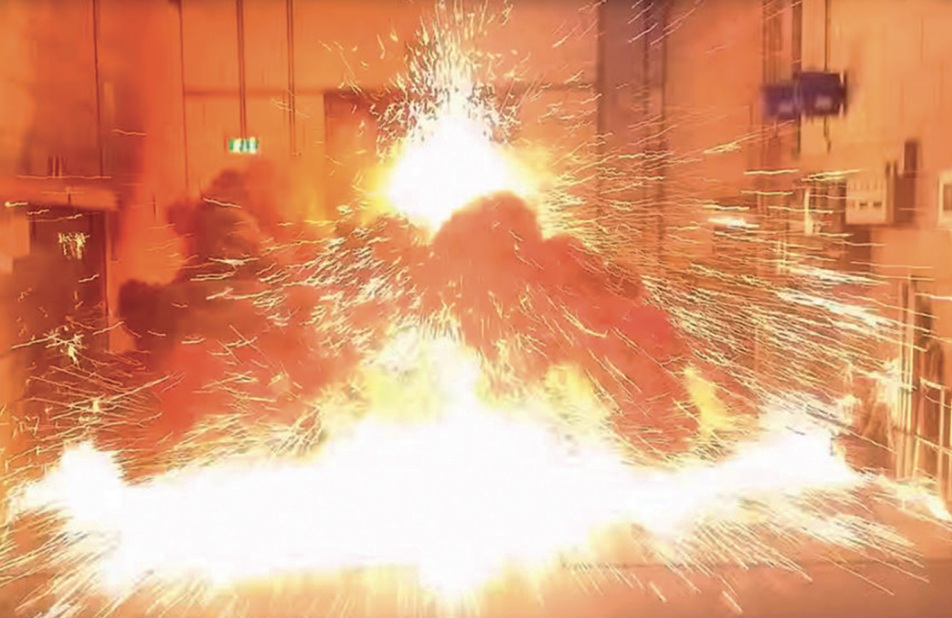
Here are the key requirements we follow for designing in hazardous areas:
Hazardous Area Classification
Zone Classification identifies and classifies the hazardous areas based on the presence and frequency of explosive atmospheres.
- Zone 0: An area where an explosive gas atmosphere is present continuously or for long periods.
- Zone 1: An area where an explosive gas atmosphere is likely to occur in normal operation.
- Zone 2: An area where an explosive gas atmosphere is not likely to occur in normal operation and, if it occurs, will exist only for a short period.
- For dust, similar zones are used: Zone 20, Zone 21, and Zone 22.
Compliance with Standards
- AS/NZS 60079 Series: Follow the AS/NZS 60079 series standards, which are harmonized with IEC 60079 standards and provide comprehensive guidelines for equipment and protective systems intended for use in explosive atmospheres.
- Hazardous Substances and New Organisms (HSNO) Act: Ensure compliance with the HSNO Act for managing hazardous substances.
Selection of Equipment
- Certified Equipment: Use only equipment certified for use in hazardous areas. Certifications should include ATEX, IECEx, or other relevant standards.
- Ingress Protection (IP) Ratings: Ensure equipment has appropriate IP ratings to prevent the ingress of dust and water.
- Temperature Classification: Select equipment with suitable temperature classifications to avoid ignition of explosive atmospheres.
Explosion Protection Techniques
- Flameproof (Ex d): Equipment designed to contain an explosion and prevent it from spreading.
- Increased Safety (Ex e): Equipment with additional safety features to prevent ignition.
- Intrinsic Safety (Ex i): Systems designed so that electrical energy is insufficient to cause ignition.
- Pressurization (Ex p): Enclosures maintained at a higher pressure to prevent explosive atmospheres from entering.
System Design Considerations
- Wiring and Cabling: Use cables and wiring methods suitable for hazardous areas, including armored cables and appropriate conduits.
- Earthing and Bonding: Implement proper grounding and bonding to prevent static electricity build-up and ensure safety.
- Sealing and Glands: Use appropriate cable glands and seals to maintain the integrity of explosion protection.
Installation Practices
- Qualified Personnel: Ensure that installations are performed by personnel trained and certified in hazardous area installations.
- Inspection and Testing: Conduct thorough inspections and testing of all equipment and installations before commissioning to ensure compliance with design specifications and safety standards.
Maintenance and Inspection
- Regular Inspections: Schedule and perform regular inspections and maintenance according to manufacturer guidelines and regulatory requirements.
- Record Keeping: Maintain detailed records of inspections, maintenance, and any modifications made to the installations.
Risk Assessment and Management
- Hazard Identification: Continuously identify and assess potential hazards in the area.
- Mitigation Measures: Implement appropriate measures to mitigate identified risks.
- Emergency Planning: Develop and maintain emergency response plans and ensure all personnel are trained in emergency procedures.
Documentation and Labeling
- Detailed Documentation: Maintain detailed documentation of all design, installation, and maintenance activities, including hazard assessments, zoning, equipment specifications, and certification records.
- Proper Labeling: Clearly label all equipment with relevant hazard classifications, certifications, and operating instructions.
Local Regulatory Engagement
- WorkSafe New Zealand: Engage with WorkSafe New Zealand, the primary regulatory authority, to ensure compliance with all relevant safety regulations and standards.
- Consultation and Approval: Seek consultation and approval from local authorities and regulatory bodies as necessary, particularly for new installations or significant modifications to existing systems.
We choose safety and take Health & Safety seriously
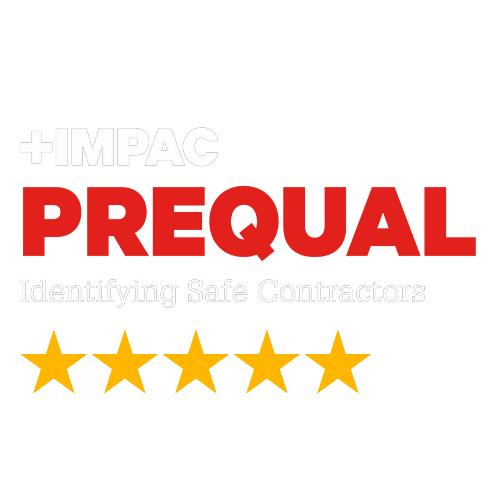
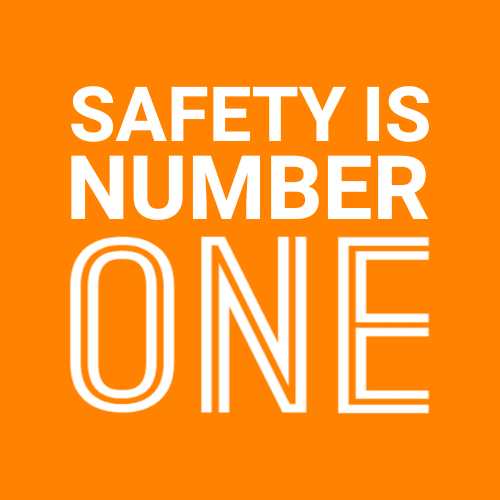
Get In Touch
SUBSCRIBE TO OUR NEWSLETTER
To receive the latest industry news and insights and our new Athenry Electrical Knowledge Series